Lean thinking is a philosophy that seeks continuous improvement, eliminating MUDA (non-added value operations) from processes. There are methods and tools for this. It can be applied in all types of businesses (not just factories). But there is logic and order in its implementation.
- Define the mission, the vision, the strategy …
- Define the “value” for customers
- Create a continuous improvement team
- Train the necessary people
- Communicate to all within the organisation
- Define the value stream (VSM / Flowchart)
- Select a pilot zone where to start implementing the tools
- Start with the basic tools
- 5S & visual management
- Standards
- KPI and line animation (autonomous team)
- Problems solving
- Carry on with the tools which are the best adapted to the points you want to improve: quality, productivity, logistic, team motivation …
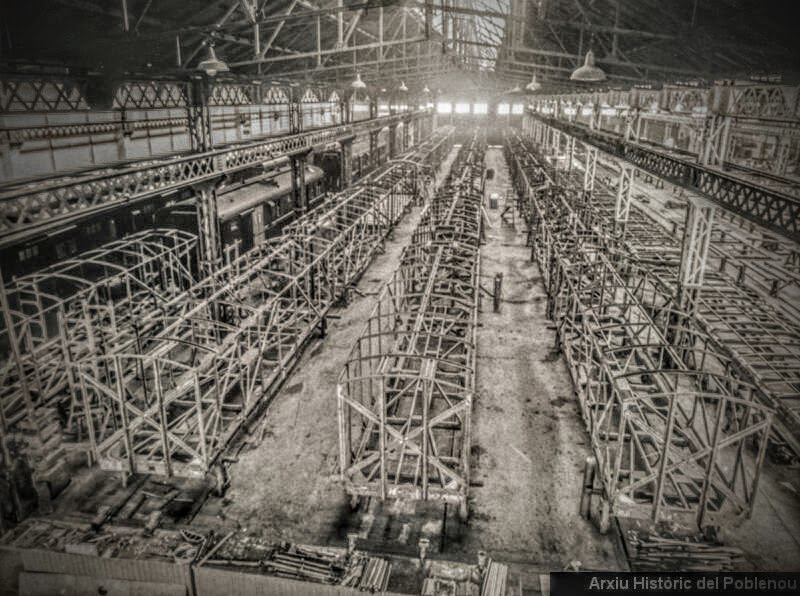
A common mistake is to embark on the way of continuous improvement by applying an isolated tool (very often the 5S). It is likely that this will help you improve, but this improvement will hardly be sustainable over time if the philosophy of continuous improvement is not known and shared by all and is not implemented consistently.
If we talk about | The tools & method we can apply are: |
General | Lean thinking: concepts & philosophy |
Flow & production line analysis | VSM / Process mapping / Lines balancing / Layout design |
Measures / Strategy | KPIs (SQCDM) / Control Panels / Hoshin-Kanri / Roadmaps / Workstation audits |
Basics | 5S / Visual management / Estándares / AIC / Cascading meetings / Autonomus team |
Quality | PokaYoke system / Andon |
Productivity | SMED / TPM |
Logistics | Pull flow / Kanban |
Continuous improvement | Methodologies for problems solving: QRQC, PDCA, 8D… / Kaizen / Gemba walk |
Motivation | Skill matrix / Suggestions for improvement / Change management |